ارزیابی سیستم هوای فشرده که توسط Draw Professional Services در تاسیسات Grundfos Pumps واقع در فرزنو کالیفرنیا انجام شد، فرصتهای بهبود قابل توجهی ایجاد کرد.
این شرکت پمپ های گریز از مرکز و قطعات هیدرولیک را در این مرکز تولید می کند.
Grundfos بزرگترین تولید کننده پمپ در جهان است که در دانمارک مستقر است و بیش از 19000 کارمند در سراسر جهان دارد.
به عنوان بخشی از اهداف شرکت Grundfos، این شرکت همیشه بر روی پایداری سیستم تولید هوای فشرده تمرکز کرده است.
این امر در سیستم هوای فشرده آنها به خوبی هم انجام می شود.
مدیریت کارخانه می خواست اطمینان حاصل کند که سیستم آنها به طور کامل بهینه شده است.
این باعث می شود اطمینان حاصل شود که انرژی تلف شده به حداقل می رسد.
این سیستم قبلاً از ترکیبی از کمپرسورهای هوا با سرعت ثابت و متغیر تشکیل شده بود که بازدهی جانبی عرضه را بسیار خوب میکرد.
نگاهی دقیق به اجزای سیستم هوای فشرده و استفاده نهایی آنها نشان داد که میتوان اصلاحات شگفتانگیزی را برای افزایش کارایی انجام داد.
این امر خود می تواند قابلیت اطمینان را بهبود بخشیده و هزینه ها را کاهش دهد.
پیش زمینه این سیستم تولید هوای فشرده
این سیستم تولید هوای فشرده از دو کمپرسور خانه مجزا،
اما به هم پیوسته در ساختمان 1 و 2 که در شکل زیر نشان داده شده است، تشکیل شده است.
یکی از دو درایو سرعت متغیر در کمپرسور خانه اصلی برای تعمیر در طول ارزیابی سیستم هوای فشرده خاموش بود.
لازم به ذکر است که همه کمپرسورها، به جز یکی، در محفظه کمپرسور درایر دارند.
خروجی هوای کمپرسورها توسط فیلترهای حذف کننده غبار و چند کوالسینگ فیلتر اضافی، فیلتر می شود.
این سیستم دارای ظرفیت گیرنده ذخیره سازی با مجموع 1700 گالن بود که در بالادست کنترل کننده فشار/فلو با کنترل پنوماتیک و حداقل ظرفیت ذخیره سازی عمومی در ساختمان دوم کارخانه قرار داشت.
برخی از مناطق تولید خاص در کارخانه 1 به فشار بالاتر از حد معمول نیاز دارند؛
بنابراین یک شیر مخصوص در سمت فشار بالای کنترل کننده فشار/فلو نصب شد تا این نیاز را تامین کند.
ارزیابی سیستم هوای فشرده نشان داد که کنترل کننده فلو به درستی تنظیم نمی شود.
همچنین باعث ایجاد مشکلات فشار در هر دو ساختمان می شود.
دیتا لاگرها به مدت دو هفته روی سیستم قرار داده شدند تا فشار سیستم در نقاط بحرانی مختلف، قدرت کمپرسور، درایر و فلو سیستم را بررسی کنند.
در طول ارزیابی سیستم هوای فشرده این کارخانه، مشاهده شد که ماشینهای مهم مختلف دورههایی از فشار کم را تجربه میکنند؛
بنابراین آزمایشهای ویژه و دقیق فشار برای تعیین علل انجام شد.
بررسی دو کمپرسور خانه مجزا
در شکل بالا دو کمپرسور خانه مجزا اما به هم پیوسته وجود دارد که هر یک در یک ساختمان هستند.
کمپرسور خانه اصلی دارای یک کنترل کننده فشار/فلو برای کاهش فشار در کارخانه بود؛
اما یک شیر آب فشار بالا نیز برای فرآیندهای تولید حیاتی کار میکرد.
کوالسینگ فیلترها باعث از دست دادن فشار بیش از حد می شدند و مشخص شد که اضافی هستند.
تجزیه و تحلیل داده های فشار این کارخانه
تجزیه و تحلیل ثبت داده های فشار (شکل زیر) نشان داد که کمپرسور درایو با سرعت متغیر، فشار تخلیه ثابت نزدیک به psi 120 را حفظ می کرد.
در حالی که فشار در نقاط بحرانی مختلف در طول عملیات تولید اوج به 85 psi کاهش یافت.
فشار عمومی در نیروگاه ها، به ویژه کارخانه 2، بین 102 و 112 psi در نوسان بود، که نشان می دهد ولو کنترل فشار/فلو به درستی تنظیم نمی شود.
همچنین کارخانه 2 فاقد حجم ذخیره عمومی کافی برای پشتیبانی از جریان های گذرا است.
پرسنل کارخانه همچنین قطع مکرر تولید را گزارش میکردند که بر توان عملیاتی کارخانه، ناشی از نوسانات فشار تأثیر میگذاشت.
ما سه دستگاه تولید را در کارخانه پیدا کردیم که به فشار تخلیه کمپرسور بالاتر از حد مطلوب نیاز داشتند.
دو مورد از این موارد صرفاً توسط فیلترهای عرضه و تنظیم کننده های کم حجم ایجاد شده اند.
فرانک موسکوویتز، حسابرس ارشد،
گفت: «زمانی که این مشکلات برطرف شد، متوجه شدیم که میتوان کل کارخانه را با فشار تخلیه 100 psi اجرا کرد.»
شکل بالا نمودارهای فشارهای مختلف سیستم بحرانی فشار، سیستم اصلی کم و متغیر را در کارخانه 2 و فشار بسیار متغیر را در ماشین های بحرانی نشان می دهد.
تست فشار ویژه هنگام ارزیابی سیستم هوای فشرده
ثبت دادههای معمولی با فرکانس نمونهبرداری آهستهتر، جزئیات لازم را برای ارزیابی مناسب تلفات فشار گذرای ناشی از اجزای کوچکتر نشان نمیدهد؛
بنابراین آزمایشهای ویژه در مناطق مشکلدار با نرخ نمونهگیری دیتالاگر بالاتر انجام شد.
شکل زیر نتایج آزمایش بر روی یک دستگاه اسکرو را نشان میدهد که با نرخ نمونهبرداری یک ثانیه انجام شده است.
افت فشار زیاد، ناشی از فیلتر منبع و تنظیمکننده کم اندازه و کمبود ظرفیت ذخیرهسازی است.
این مشکل تنها زمانی ظاهر میشود که دستگاه در حال مصرف هوا باشد.
حال هنگامی که جریان متوقف میشود، برطرف میشود که با مراحل کم فشار بالا نشان داده میشود.
اندازه مناسب این اجزای منبع تغذیه و افزودن مقداری ظرفیت گیرنده ذخیره محلی کوچک و تقویت کننده فشار مشکل را رفع می کند.
همانطور که در شکل بعدی (شکل دوم در زیر) نشان داده شده است، مشکل را اصلاح کرد.
همچنین اجازه داد فشار تخلیه کمپرسور کاهش یابد.
هنگامی که این دستگاه اسکرو شروع به مصرف هوا می کند، فشار به طور قابل توجهی کاهش می یابد.
همچنین باعث مشکلات تولید می شود.
این امر پرسنل کارخانه را مجبور به افزایش فشار تخلیه کمپرسور کرد که باعث هدر رفتن انرژی می شود.
اندازه صحیح فیلتر، رگولاتور، اجزای لوبریکنت و نصب انبارهای کوچک محلی افت فشار را کاهش می دهد.
همچنین اجازه می دهد فشار تخلیه کمپرسور کاهش یابد.
نتایج ارزیابی سیستم هوای فشرده در این کارخانه
تجزیه و تحلیل داده های جمع آوری شده دیتاهای پایه زیر را نشان داد:


یک بازرسی کامل ماشین به ماشین تعدادی از کاربردهای بالقوه نامناسب از جمله دمیدن هوا و تولید خلاء را نشان داد.
حدود 275 cfm فلو غیر تولیدی در طول عملیات آخر هفته مشاهده شد که بیشتر آن به نشت نسبت داده می شود.
کاهش هزینه های عملیات و تثبیت فشار کارخانه
تحقیقات و محاسبات دقیق نشان داد که موارد زیر را می توان برای کاهش قابل توجه هزینه های عملیاتی و تثبیت فشار کارخانه انجام داد.
البته چیدمان نهایی کمپرسور خانه ها که کنترل هماهنگ را در فشار 100 psi کمتر نشان می دهد.
بررسی نتیجه این محاسبات:
- از یک سکانسر (Sequencer) خودکار برای مرحله بندی کمپرسورها استفاده کنید و فشار هدف کمتری را در حدود psig 100 تنظیم کنید.
سکانسر بهطور خودکار کمپرسورهای پشتیبان را در صورت خرابی هر واحد اصلی راهاندازی میکند. - نازل های دمنده را در چهار دستگاه برای ایر کولینگ قطعات با فن های خنک کننده هوای موتوری تعویض کنید.
- یک تقویت کننده پنوماتیکی برای کاربردهای پرفشار بخرید و نصب کنید که به بقیه نیروگاه اجازه می دهد در فشار نقطه تنظیم پایین تر کار کنند.
- رگولاتورهای موجود برای ماشین های اسکرو را با رگولاتورهای فلو بالا جایگزین کنید.
برای پشتیبانی از فشار، مخازن موج کوچک اضافه کنید. - کوالسینگ فیلتر ثانویه در پد اصلی را بردارید.
- ولو کنترل جریان فشار را بردارید یا آن را در لنت اصلی دور بزنید.
- یک گیرنده 2560 گالنی خریده و نصب کنید تا به عنوان ولوم گیرنده جانبی خشک برای تثبیت فشار در کارخانه 2 استفاده شود.
- برای تثبیت فشار ناشی از جریان بالا، مخزن ذخیره 650 گالن را در یک سندبلستر بزرگ اضافه کنید.
- لوله های پلاستیکی دمنده باز را با نازل های مهندسی شده جایگزین کنید.
این ضربه مورد نیاز را با کاهش جریان هوا حفظ می کند. - آگاهی کارکنان در مورد هزینه های تولید هوای فشرده را افزایش دهید.
آنها باید در صورت عدم نیاز تجهیزات را خاموش کنند.
اتوماسیونی مانند ولوهای برقی که هوا را در صورت عدم استفاده قطع می کنند را بررسی کنید. - یک دستگاه نشت یاب بخرید و از آن برای کاهش ضایعات متمرکز استفاده کنید.
نشت هوا را تا 50 cfm کاهش دهید (فقط یک نقطه شروع).
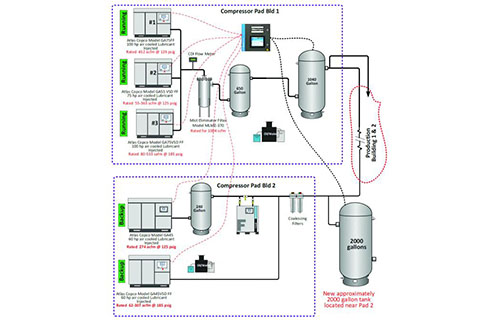
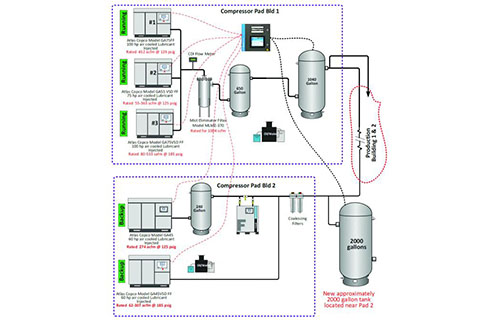
محاسبات پس انداز بالقوه در بازرسی سیستم هوای فشرده
بر اساس معیارهای توصیه شده اصلی، پساندازهای تخمینی برای اقدامات مختلف که توسط برنامه AirMaster+ محاسبه شده است، در جدول زیر آمده است:


توصیه های گزارش ارزیابی سیستم هوای فشرده نشان داد که با کاهش فشار تخلیه، کنترل بهتر کمپرسورها و کاهش ضایعات هوای فشرده، صرفه جویی قابل توجهی امکان پذیر است.
در حال حاضر پروژه رو به اتمام است و برآوردهای اولیه نشان میدهد که کاهش فشار دبی و کاهش فلو، توان ویژه کمپرسورها را از 20.2 کیلووات بر متر مکعب به سطح جدید 18.2 کیلووات بر متر مکعب تغییر داده است تا حدود 10 درصد در مصرف انرژی کاهش یابد.
در واحد خروجی به طور کلی، کاهش انرژی، از جمله کاهش جریان در حال حاضر از سطح 20 درصد عبور می کند.
همچنین انتظار می رود به سطوح بالاتر هم افزایش یابد.
علاوه بر این، سیستم قابل اعتمادتر شده است؛
زیرا در حال حاضر به اندازه کافی پشتیبان شروع خودکار وجود دارد.
تا خرابی هر یک یا حتی دو کمپرسور اصلی را برطرف کند.
یکی از بهترین مزایای همه این تغییرات، افزایش پایداری فشار بر روی ماشینهای حیاتی و سایر مناطق تولیدی است.
قطعات جدید با اندازه مناسب و گیرندههای ذخیرهسازی محلی بزرگ تضمین میکنند.
این باعث می شود که تولید بدون مشکل ادامه مییابد و این امکان را برای Grundfos فراهم میکند که محصولات بیشتر و بهتری را در سالهای آینده تولید کند.
نتیجه گیری این ارزیابی سیستم هوای فشرده
نتایج این ارزیابی سیستم هوای فشرده نشان میدهد که داشتن کمپرسورهای VSD و کنترل فشار، تضمینی برای کارایی بالا نیست.
همیشه بهترین کار این است که یک بازرس هوای فشرده متخصص، سیستم شما را با اندازهگیری دقیق با ثبتکنندههای داده و انجام یک بررسی دقیق کارخانه ارزیابی کند.
اغلب،
شرایط غیرمنتظره ای آشکار می شود که در صورت اصلاح، مزایای قابل توجهی برای توان تولید کارخانه و هزینه های انرژی به همراه خواهد داشت.
Moskowitz
میگوید: «من از تیم بهبود هوای فشرده در Grundfos بسیار تحت تأثیر قرار گرفتهام، ما سالانه ارزیابیهای هوای فشرده زیادی را انجام میدهیم، اما بسیار نادر است که مشتری با انجام همه توصیههای ما موافقت کند و همچنین موارد بیشتری از خودشان هم ارائه کند.»
ما خوشحالیم که به متخصصان در این زمینه اعتماد کردیم تا به ما بگویند چگونه سیستم های هوایی خود را بهبود دهیم.
می دانستم که در مسیر درستی هستیم و نتایج هم این را نشان می دهند.
Sean Wolfe، مدیر APU در Grundfos،
گفت: “ما به بهبود در کنترل کمپرسور خود ادامه می دهیم، تلاش های خود را برای کاهش نشتی ها گسترش داده ایم و اکنون با یک برنامه تعطیلی آخر هفته برای کاهش انرژی (در زمان خاموشی خود) جلو می رویم. ”
One thought on “داستان صرفه جویی با ارزیابی سیستم هوای فشرده در Grundfos”