نظارت بر سیستم هوای فشرده کارخانه های دارویی مطابق با GMP
گازهای فشرده که به طور مستقیم در جریان مواد دارویی و کنترل فرآیند مورد استفاده قرار میگیرند، نیازمند سطح بالایی از توجه و ادغام مداوم در سیستم شیوههای تولید خوب (GMP) فناوری اتاق تمیز هستند.
اگر تامین نیتروژن فشرده از یک مرکز ذخیرهسازی (گازی در مخازن تحت فشار یا به شکل نیتروژن مایع با تبخیر بعدی) همچنان از نظر کیفی توسط گواهی تجزیه و تحلیل (CoA) از سازنده نیتروژن تضمین شود، برای هوای فشرده تولید شده در محل دشوارتر میشود:
فشردهسازی با استفاده از هوای محیط به عنوان منبع انجام میشود که میتواند در مکانهای مختلف بسیار متفاوت باشد یا به شدت تحت تأثیر عوامل محیطی قرار گیرد که تأثیر مستقیمی بر کیفیت دارد.
تنها تصفیه در توزیع بیشتر میتواند کیفیت مناسبی تولید کند. برای تسلط بر این شرایط کلی، یک مشخصه که با دقت با کاربرد مرتبط باشد، یک فناوری پردازش و توزیع معتبر و بالاتر از همه، یک نظارت مبتنی بر استفاده از مشخصات با نظارت همراه با تأیید بعدی برای استفاده روی یا در محصول مورد نیاز است.
این مقاله قصد دارد روابط بین ریسکها و مشخصات، فرصتها و مسئولیت در اعتبارسنجی، و به ویژه استفاده از فناوری اندازهگیری مدرن و کالیبره شده در زنجیره نمونه را نشان دهد.
هوای فشرده در محیط دارویی
هوای فشرده یک “ماده گرانبها” است، نه تنها زمانی که به هزینههای استفاده از انرژی برای راهاندازی شبکه هوای فشرده به شیوهای مطمئن نگاه کنید. ارزشمند نیز به دلیل اینکه هوای فشرده اغلب بسیار نزدیکتر از آنچه انتظار میرود به محصول (یا داخل) میرسد.
بهطور خاص، این شامل فرآیندهایی مانند دمیدن بستهبندی اولیه، انتقال محصولات از ظرف به سوزن پرکننده در شرایط آسپتیک، خشک کردن ظروف، یا تخلیه پس از خلاء بالا در لیوفیلیزرها یا تخمیرکنندهها است.
هوای فشرده تأثیر بسیار محدودی بر محصول دارد و بنابراین به سطح بسیار بالایی از توجه در سیستم GMP (1،2) نیاز دارد.
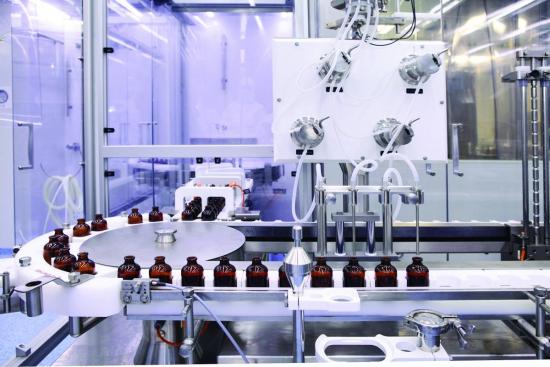
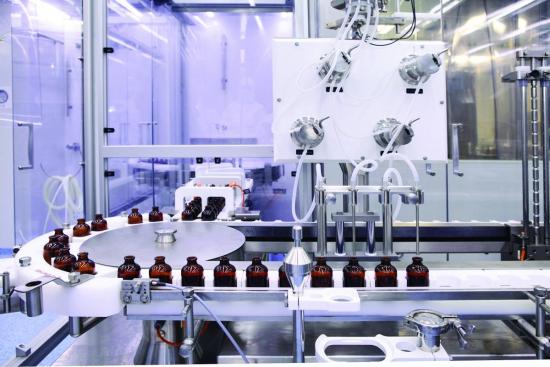
در بسیاری از گزارشهای بازرسیهای رسمی، اغلب انتقاد میشد که نه مشخصه روشنی، نه یک صلاحیت پایدار، یا مدیریت GMP در مورد عملیات گازهای فشرده انجام شده است.
بهطور خاص، ایجاد مشخصه انجام نشده بود یا فقط ناکافی انجام شده بود. دلیل این امر مطمئناً این است که برخلاف رسانههای مایع، مانند آب خالص یا آب برای تزریق، هیچ مشخصه روشنی توسط دارونامه اروپایی (Ph. Eur.) وجود ندارد.
مشخصه “هوای دارویی” که در Ph. Eur. یافت میشود، برای مشخصه هوای فشرده نامناسب است زیرا هوای تنفسی ارائه شده به بیمار را با معیارهای پذیرش توصیف میکند. ارجاع به ISO 8573 (3) از سازمان بینالمللی استانداردسازی تنها کاربرد محدودی دارد زیرا در اینجا طبقهبندی مقادیر حدی برای غلظت ذرات، نقطه شبنم فشار و محتوای روغن تعریف شده است، اما توصیه نمیشود که در کدام کاربرد دارویی و کدام کلاس یا مشخصه لازم است و باید مورد استفاده قرار گیرد.
ISO 8573 همچنین چیزی در مورد مشخصات احتمالی میکروبهای موجود در هوا مشابه ضمیمه 1 دستورالعملهای GMP اتحادیه اروپا نمیگوید.
این واقعیت به عنوان یک روند در ماههای اخیر در جریان بازرسیهای رسمی مورد توجه قرار گرفته است. گازهای فشرده نیتروژن و هوای فشرده بنابراین به کانون نظارت تبدیل شدهاند.
بسیار بیشتر: نظر رسمی در مورد ارزیابی تعهدات GMP برای سیستمهای هوای فشرده در “Aide memoire – Monitoring of Sterile Manufacturers” دفتر مرکزی ایالات فدرال برای حفاظت از سلامت در آلمان (4) منتشر شد که بیان میکند:
“هنگام تعیین هوای فشرده که با محصول یا سطوح در تماس با محصول تماس پیدا میکند، موارد زیر باید رعایت شود: علاوه بر نوع محصولات تولید شده، ارزیابی ریسک باید طراحی سیستم و کیفیت هوای خروجی را نیز در نظر بگیرد.”
در ارتباط با ارزیابی هیدروکربنها، باید توجه داشت که آلودگی با روغن در هوای فشرده، مخلوطی از آئروسلهای نفت، بخار نفت و سایر هیدروکربنها است. بنابراین تعریف “روغن” به عنوان مخلوطی از هیدروکربنها با ≥ 6 اتم C (ISO 8573-1:2010) مناسب است. روشهای اندازهگیری و اجزای روغن ثبت شده باید بنابراین روشن شوند.
نظارت بر هیدروکربن همچنین برای کمپرسورهای هوای بدون روغن ضروری است، زیرا آلایندههای مربوطه نیز از طریق هوای ورودی وارد میشوند.
پارامترهای خلوص زیر که در ISO 8573 توضیح داده شده است باید در نظر گرفته شوند:
- حدود برای شمارش باکتری / ذرات انتظار میرود.
- نظارت آنلاین آب و هیدروکربنها ممکن است ضروری باشد، بهویژه برای سیستمهایی که به دلیل استفاده از خشککنهای تبرید یا کمپرسورهای هوا با خنککننده روغن، خطر بالاتری برای عدم انطباق با الزامات مشخصه دارند.
با این روشنسازی محدودیتهایی بر اساس ISO 8573 همانطور که تعریف شده وجود ندارد، اما جهت مشخص است. برای تعریف مشخصه اکنون توصیه میشود طبقهبندی بر اساس انجمن تولیدکنندگان ماشینآلات و کارخانههای آلمان (VDMA) بسته به کاربرد (اهمیت برای محصول) انجام شود.
بهعنوان مثال، هنگام استفاده در منطقه استریل، “تماس مستقیم هوای فشرده با مواد بستهبندی استریل (هوای فرآیند)،” در برگه استاندارد VDMA 15390 (5) با معیارهای پذیرش زیر تعریف شده است:
- حداکثر اندازه ذرات و چگالی آلایندههای جامد: کلاس 1، مربوط به 0.1 میکرومتر و 0.1 میلیگرم بر متر مکعب است.
- نقطه شبنم فشار در دمای محیط > + 10 درجه سانتیگراد: کلاس 4، مربوط به + 3 درجه سانتیگراد Td است.
- نقطه شبنم فشار در دمای محیط <+ 10 درجه سانتیگراد: کلاس 2/3، مربوط به -40 درجه سانتیگراد Td / -20 درجه سانتیگراد Td است.
- حداکثر محتوای روغن: کلاس 1، مربوط به 0.01 میلیگرم بر متر مکعب است. استریلیته: بله
خطرات آلودگی در هوای فشرده
به عنوان دلیل اصلی ایمنی در استفاده از هوای فشرده در محیط GMP، بارها در شرایط بازرسی توسط بازرسان نشان داده شده است که استفاده از “کمپرسورهای هوای بدون روغن” برای اطمینان از هوای فشرده واجد شرایط و بدون آلودگی کافی است.
متأسفانه، این یک اشتباه است زیرا خطر آلودگی اغلب به طور قابل توجهی بیشتر از آنچه انتظار میرود یا شناخته شده است. به طور ساده میتوان آن را به دو بخش تقسیم کرد:
- آلودگی فعال در تصفیه هوای فشرده
- آلودگی غیرفعال هوای فشرده توسط سیستمهای مصرفکننده هوای متصل
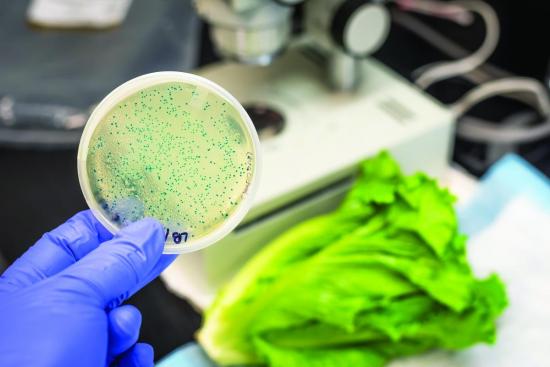
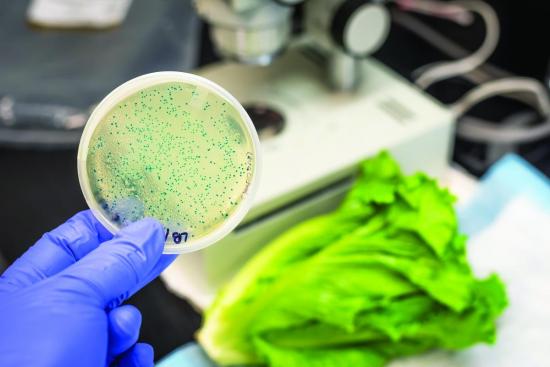
در مورد آلودگی فعال، علت اصلی آلودگی در استفاده از کمپرسورهای هوا با خنککننده روغن یافت میشود. اما فراتر از آن، یکی از آلایندههای دیگر باید در هوای محیطی تنفسشده جستجو شود.
بسته به موقعیت دهانههای ورودی هوا، مقدار قابل توجهی از ذرات و آلایندههای نفتی به شکل آئروسلها میتوانند از محیط وارد و فشرده شوند. آلودگی (بیشتر جزئی) به شکل ذرات و محتوای روغن از قسمتهای متحرک یک کمپرسور هوا، بهویژه پس از یک دوره کار طولانی، همچنین باید در نظر گرفته شود.
علاوه بر این، رطوبت زیادی از هوا میآید و در نتیجه ورود بالقوه میکروبهای موجود در هوا به سیستم در حال کار و در نتیجه به شبکه خط لوله وارد میشود. در مورد آلودگی غیرفعال، خطر برای کیفیت هوای فشرده این است که به دلیل عوامل همزمانی نامطلوب یا ابعاد ناکافی لوله، “مصرفکنندگان بزرگ” باعث برگشت فشار بیش از حد در سیستم خط هوایی فشرده به سمت سیستم خلاء شوند.
در مورد تهویه استریل با استفاده از هوای فشرده، بهعنوان مثال ظروف که پس از فروپاشی فاز بخار، پس از استریلیزاسیون با بخار به فاز خلاء میافتند، یا هنگامی که خلاء بالای لیوفیلیزرها با باز شدن شیر به خط هوایی فشرده میشکند، شرایط فشار در سیستم خط معکوس میشود.
خطر اصلی در اینجا این است که میتواند در شرایط “بدترین حالت” رخ دهد که چنین فشار منفی بزرگ و موقتی در شبکه هوای فشرده ایجاد شود که آلودگی مجدد به سیستم از طریق خطوط هوایی فشرده از مناطق عملیاتی دیگر رخ دهد. هنگام طراحی شبکههای هوای فشرده، این باید بهطور قطعی مبتنی بر ریسک بررسی و برنامهریزی شود یا در فرآیند کنترل تغییرات داخلی قبل از اتصال مصرفکنندگان جدید در نظر گرفته شود.
برای جلوگیری از چنین اثراتی، استفاده از مدارهای به اصطلاح “block & bleed” و یا نصب شیرهای یکطرفه در خط هوایی فشرده میتواند در نظر گرفته شود. در هر صورت، این واقعیت نیز باید بهعنوان بخشی از صلاحیت نصب (IQ) / صلاحیت عملیاتی (OQ) شبکه مشمول GMP بررسی شود.
چه آلودگی فعال یا غیرفعال: در شبکههای هوای فشرده اغلب بسیار گسترده در یک کارخانه داروسازی، این اصل اعمال میشود: “آنچه در شبکه است در آنجا باقی میماند!”
در اکثر موارد، تمیز کردن امکانپذیر نیست، یا اغلب در جریان برنامهریزی خطوط هوایی در نظر گرفته نمیشود.
برای اینکه سطح آلودگی در داخل خط هوایی فشرده قابل مشاهده/کنترل باشد، بنابراین توصیه میشود که یک لوله به اصطلاح “بازرسی” نصب شود، یعنی بخشی تقریباً 50 تا 100 سانتیمتر (سانتیمتر)، که میتوان آن را با استفاده از اتصالات سه گیره بهعنوان بخشی از نگهداری برنامهریزیشده برداشت و بازرسی کرد.
در موارد شدید، درجه آلودگی میتواند منجر به بازسازی جزئی یا کامل یا جایگزینی شبکه هوای فشرده شود.
صلاحیت سیستم هوای فشرده و توزیع
یکی از سوالات پرتکرار درباره سیستمهای هوای فشرده، نیاز به تأیید صلاحیت کامل همه اجزای تولید و توزیع هوای فشرده است. اولین چالش اینجاست که برخلاف یک کارخانه فرآیند (مثل خط پر کردن محصولات استریل)، برنامهریزی مطابق با GMP با در نظر گرفتن “طراحی بهداشتی” برای یک کمپرسور هوا تقریبا غیرممکن است. حتی اگر کمپرسورهای هوا گاهی اوقات توسط سازنده بهعنوان “مطابق با GMP” معرفی شوند، که اشاره به عملکرد بدون روغن دارد، این معمولاً فقط به نبود خنککننده روغنی و کاهش قطعات روغنی محدود میشود.
بنابراین، یک رویه شناخته شده GMP این است که کمپرسور هوا، همراه با نصب آن، از نظر مناسب بودن فنی تحت قوانین شیوههای مهندسی خوب (GEP) بررسی شود، تمام مدارک فنی مرتبط ارائه شود و راهاندازی موفق نیز مستند گردد. در این زمینه، یک صلاحیت کلاسیک IQ/OQ به نظر نامناسب میآید. این باید در طرح جامع اعتبارسنجی (VMP) شرکت GMP تحت عنوان “GMP در مقابل GEP” (6) فهرست یا تعریف شود.
این رویکرد در سال 2014 توسط ISPE پذیرفته شد و در انجمن بینالمللی مهندسی داروسازی (ISPE) به شرح زیر اظهار نظر شد: “تولید گاز معمولاً از شیوههای مهندسی خوب (GEP) پیروی میکند. برای اطلاعات بیشتر به ISPE Good Engineering Practice مراجعه کنید. گاز یک محصول دارویی نیست و نیازی به تولید آن بر اساس شیوههای تولید خوب ندارد.” (6)
با این حال، از نظر GMP، آمادهسازی کیفی هوای فشرده بسیار مهم است، به شرطی که تأثیر منفی بر مشخصات انتخابشده نداشته باشد و برای استفاده در منطقه فرآیند مرتبط با محصول مورد استفاده قرار گیرد. مناسب بودن تمام اجزای مورد نیاز برای آمادهسازی و توزیع در طول مراحل طراحی-صلاحیت (DQ)، IQ و OQ، از جمله یک صلاحیت عملکرد کافی (PQ)، بخش اجباری از صلاحیت/اعتبارسنجی است و بهعنوان یک پیامد GMP مشمول انحراف یا سیستم مدیریت تغییر است.
در تشابه با رویکرد GMP/GEP، توزیع و پردازش هوای فشرده، که منحصراً برای استفاده فنی خارج از اتاق تمیز استفاده میشود و به معنای هیچ تماس مستقیم یا غیرمستقیم با محصول نیست، میتواند دوباره بهعنوان یک سیستم GEP در نظر گرفته شود و بنابراین مشمول قوانین صلاحیت رسمی نمیشود.
باید توجه ویژهای در طول صلاحیت به تجهیزات فرآیند متصل/مصرفکنندگان هوا شود. اینجا نیز باید اطمینان حاصل شود که شرایط بالقوه فشار بیش از حد یا خلاء در فرآیند هیچ تأثیر منفی بر سیستم هوای فشرده به لولهکشی داخلی سیستم به دلیل خطر برگشت آلایندهها به سیستم لولهکشی ندارد.
مرز سیستم برای صلاحیت در سیستم هوای فشرده باید نقطه انتقال به سیستم فرآیند باشد، بهعنوان مثال، سنسور نظارت بر فشار یک سیستم فرآیند نیز برای صلاحیت بررسی میشود و در صورت لزوم باید تحت کالیبراسیون منظم قرار گیرد.
بازرسی کیفیت/نمونهبرداری
با طبقهبندی هوای فشرده بهعنوان یک محیط حیاتی در استفاده دارویی، بررسی منظم کیفیت هوای فشرده مطابق با مشخصه داخلی بخش اجتنابناپذیری از سیستم اعتبارسنجی است: همانند سیستمهای آب دارویی، یک طرح نمونهبرداری نیز باید بهعنوان بخشی از PQ برای عملیات مداوم پس از راهاندازی تهیه شود.
تعداد نقاط نظارت و فرکانس نمونهبرداری باید بر اساس تحلیل ریسک تعیین و برنامهریزی شود. این میتواند شامل، بر اساس کاربرد هوای فشرده، پیچیدگی سیستم توزیع (مثلاً طول، انشعاب) یا اتصال به ریسکهای آلودگی احتمالی باشد.
در هر صورت، نمونهبرداری باید به گونهای انجام شود که به خودی خود ایمن باشد و بدون خطر آلودگی خارجی ناخواسته. روش اندازهگیری انتخابشده باید به گونهای انتخاب شود که مشخصههای تعریفشده بتوانند در واقع مطابق با GMP تعیین شوند. نکته آخر بهطور خاص دقیقاً آسان نیست، زیرا برای پارامترهای فردی ذرات، رطوبت و محتوای روغن، و همچنین یک نمونه ایمن برای میکروبهای موجود در هوا. این نیاز به تعداد زیادی از فناوریهای اندازهگیری مختلف و روشهای نمونهبرداری دارد.
با توجه به چالشهای موجود، استفاده از دستگاه اندازهگیری مناسب برای نظارت بر پارامترهای فیزیکی سیستمهای گاز فشرده مهم است. بهعنوان مثال، دستگاهی که توسط شرکت آلمانی CS INSTRUMENTS برای اندازه گیری میزان بخارات روغن در هوای فشرده ساخته شده است، امکان اندازه گیری دیجیتال روغن را از کمتر از مقادیر کلاس 1 استاندارد ISO8573-1 را دارد که می تواند پس از اندازه گیری، گزارش ها فراخوانی شود و آنالیز های لازم بر روی آن صورت گیرد و نتایج آن کاملا معتبر است.
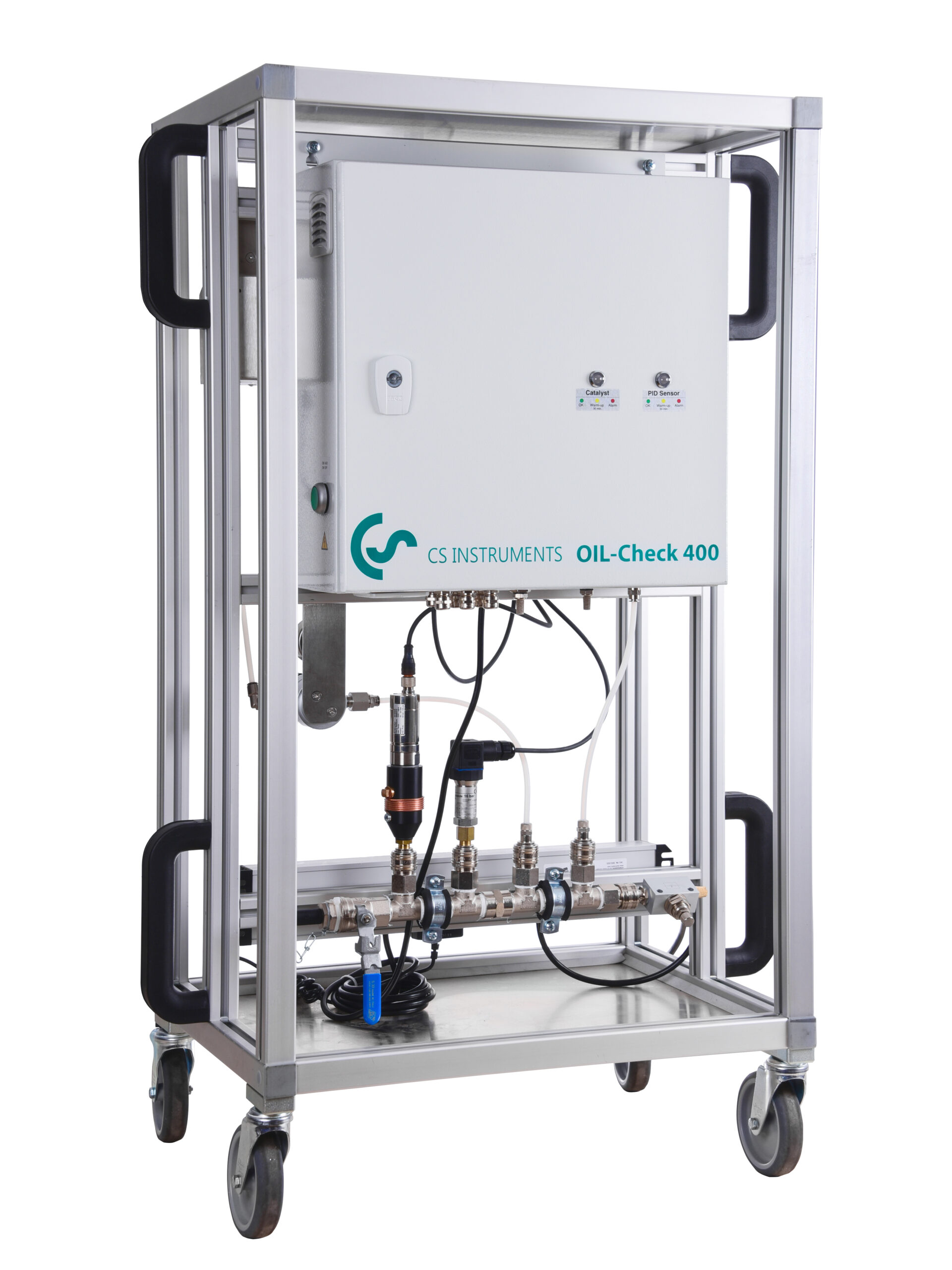
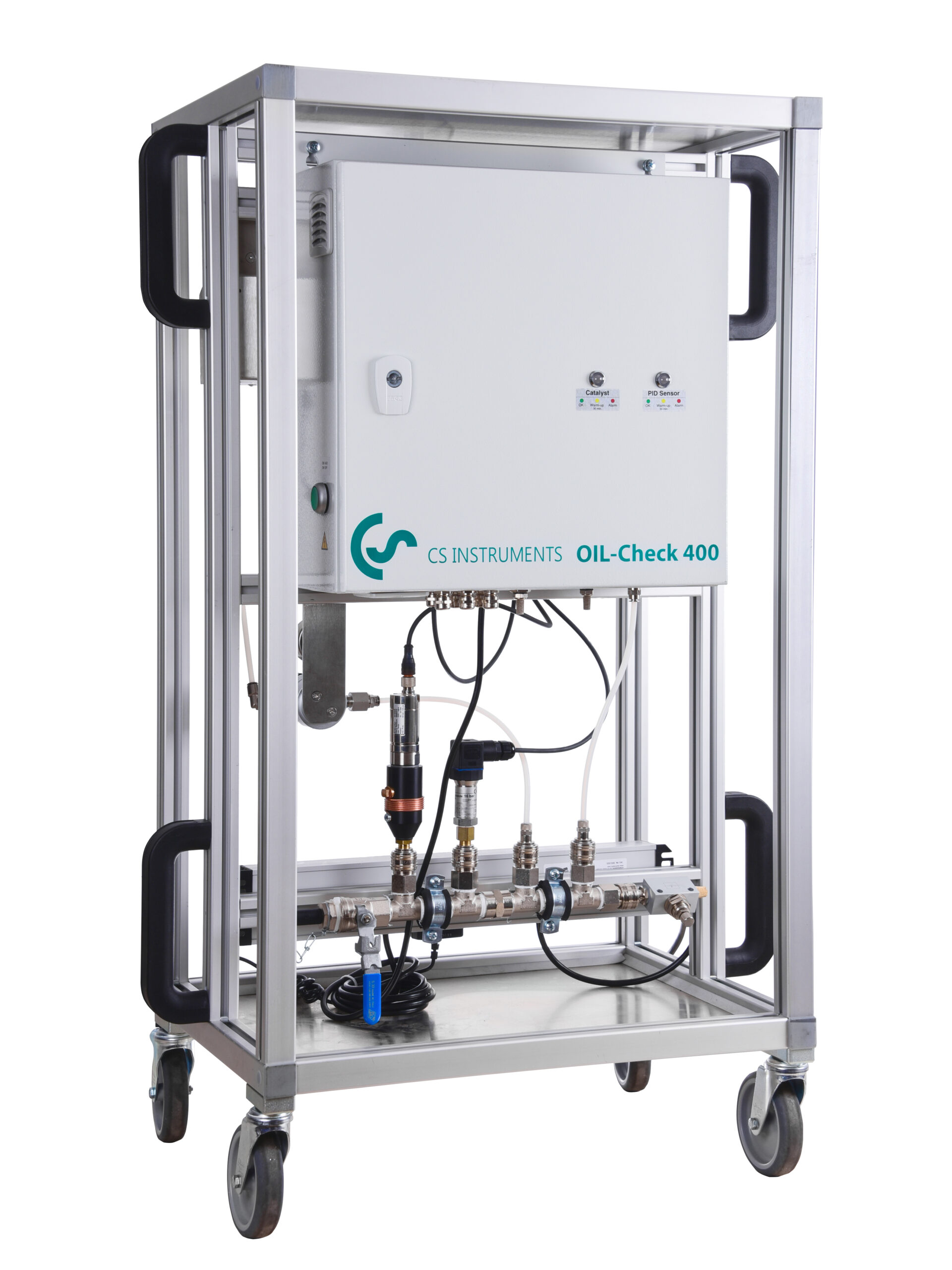
تضمین عملکرد سنسورها
یکی از چالشهای اصلی در ارتباط با فناوری اندازهگیری برای بازرسی کیفیت گازهای مطابق با GMP، تضمین عملکرد سنسورها است. در اینجا نیز، یک الزام اساسی GMP این است که سنسورهای اندازهگیری مورد استفاده تحت کالیبراسیون منظم قرار گیرند. در اینجا مهم است که قابلیت ردیابی به استاندارد ملی را تضمین کنید که در آن همه دستگاههای اندازهگیری باید به این نمونه با بالاترین دقت یک متغیر اندازهگیری شده فیزیکی قابل ردیابی باشند. تمام کالیبراسیونهای انجامشده باید با الزامات دستورالعملهای EU-GMP مطابقت داشته باشد و باید به طور کامل مطابق با شیوه مستندسازی خوب ثبت شود.
تضمین تولید ایمن
GMP در سیستمهای هوای فشرده تعامل مبتنی بر ریسک بین تعریف پارامترهای کیفیت و اجرای آنها در یک فناوری مناسب برای تولید و توزیع است. اما تنها صلاحیت مطابق با GMP و نمونهبرداری منظم میتواند اطمینان حاصل کند که از خطر آلودگی دارو جلوگیری میشود.
منابع
1) راهنمای EG GMP، پیوست 1 “ساخت داروهای استریل”، مارس 2009.
2) راهنمای EG GMP، پیوست 15 “صلاحیت و اعتبارسنجی”، اکتبر 2015.
3) ISO 8573-1:2010.
4) ZLG Aide Memoire 07120604 “Monitoring Sterile Manufacturers”، ژانویه 2015.
5) ورق استاندارد VDMA 15390-1، دسامبر 2014.
6) ISPE “Good Practice Guide Process Gases”، جولای 2011.
برای کسب اطلاعات بیشتر در مورد دستگاه های حذف CO2 ، لطفاً با ما تماس بگیرید.
ما مشتاقانه منتظر کمک به شما در یافتن راه حلی مناسب برای نیازهای خاص شما هستیم!