چرا انتخاب هوشمندانه تجهیزات ابزار دقیق حیاتی است؟
در قلب هر پروژه صنعتی موفق، انتخاب و استقرار دقیق تجهیزات ابزار دقیق نهفته است. این تصمیم، بیش از یک انتخاب ساده فنی، تضمینکننده عملکرد بهینه، افزایش بهرهوری، کاهش ریسکها و کنترل موثر فرآیندها است. هرچه کیفیت و دقت ابزارهای انتخابی بالاتر باشد، سیستمهای صنعتی با کارایی و پایداری بیشتری به فعالیت خود ادامه میدهند. این مقاله با هدف ارائه یک راهنمای جامع و یونیک، شما را در مسیر انتخاب تجهیزات ابزار دقیق مناسب برای پروژهتان یاری میکند. با بهرهگیری از این دانش، میتوانید با اطمینان کامل و دقت بینظیر، سرمایهگذاری خود را در این حوزه بهینه سازید و از هزینههای اضافی و خطرات احتمالی پیشگیری کنید.
اهمیت بی بدیل انتخاب صحیح ابزار دقیق در صنعت
تجهیزات ابزار دقیق، شامل سنسورها، ترانسمیترها، کنترلرها و رکوردرها، ستون فقرات پایش و کنترل فرآیندهای صنعتی را تشکیل میدهند. این ابزارها، به مثابه “چشم و گوش” سیستم، دادههای حیاتی را از وضعیت ماشینآلات و فرآیندها جمعآوری کرده و به سیستم کنترل مرکزی ارسال میکنند. سنسورها وظیفه اندازهگیری پارامترهای کلیدی نظیر دما، فشار، سطح و جریان را بر عهده دارند و دادهها را به ترانسمیترها منتقل میکنند تا به سیگنالهای قابل پردازش تبدیل شوند. این سیگنالها سپس به کنترلرها ارسال میشوند تا تصمیمات لازم برای پایش و بهینهسازی فرآیندها اتخاذ گردد. رکوردرها نیز با ثبت و مستندسازی دادههای فرآیند، امکان تحلیل دقیق و ارزیابی عملکرد سیستم را فراهم میآورند.
تصمیمگیری اشتباه در انتخاب هر یک از این اجزا میتواند عواقب جبرانناپذیری در پی داشته باشد. از افت شدید بهرهوری و کاهش کیفیت محصول گرفته تا خرابیهای گسترده تجهیزات و بروز حوادث ایمنی جدی. برای مثال، استفاده از سنسوری با دقت ناکافی یا بازه اندازهگیری نامناسب، به خطای اندازهگیری پارامترها و در نتیجه تصمیمگیریهای نادرست توسط کنترلرها منجر میشود. این اشتباهات نه تنها مصرف انرژی را افزایش داده و کیفیت نهایی محصول را کاهش میدهند، بلکه میتوانند مخاطرات جدی ایمنی را نیز در پی داشته باشند. از این رو، انتخاب صحیح تجهیزات ابزار دقیق باید با تحلیل دقیق نیازهای فرآیندی، شرایط عملیاتی و استانداردهای ایمنی صورت گیرد.
فراتر از جنبههای فنی، انتخاب ابزار دقیق مناسب به ارتقاء ایمنی کارکنان و کاهش ریسکهای احتمالی در محیط کار نیز کمک شایانی میکند. تجهیزات با کیفیت و مطابق با استانداردها میتوانند از بروز حوادث ناشی از نقص در اندازهگیری یا کنترل جلوگیری کرده و هزینههای تعمیر و نگهداری را به حداقل برسانند. انتخاب ابزارهایی که به طور خاص برای شرایط عملیاتی و فرآیندی دشوار طراحی شدهاند، نه تنها عمر مفید تجهیزات را افزایش میدهد، بلکه به کاهش چشمگیر هزینههای مرتبط با خرابیها و تعمیرات ناخواسته منجر میشود. این رویکرد، نه تنها عملکرد فرآیند را بهبود میبخشد، بلکه به افزایش بهرهوری کلی و کاهش هزینههای عملیاتی در بلندمدت نیز کمک فراوانی میکند.
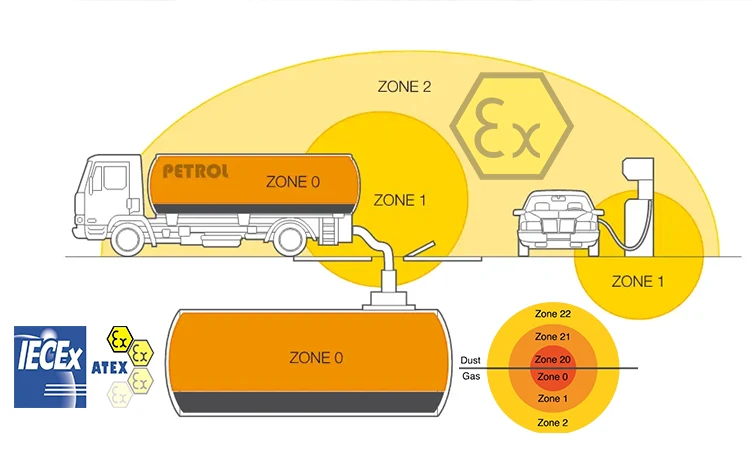
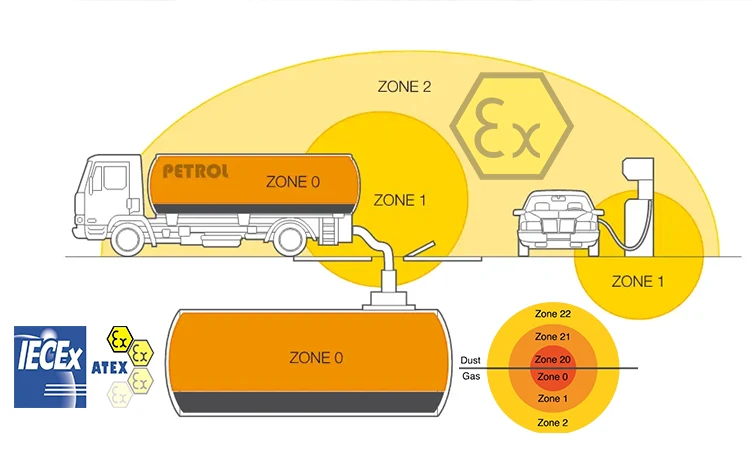
فرآیند گام به گام انتخاب تجهیزات ابزار دقیق: از تحلیل تا اجرا
برای انتخاب صحیح و بهینه تجهیزات ابزار دقیق، پیمودن مراحل زیر به صورت گام به گام ضروری است:
۱. تحلیل جامع نیازمندیهای پروژه: سنگ بنای انتخاب صحیح
اولین و مهمترین گام در انتخاب تجهیزات ابزار دقیق، تحلیل دقیق و همهجانبه نیازمندیهای پروژه است.
این تحلیل باید شامل بررسی جزئیات عوامل فیزیکی و محیطی (مانند دما، رطوبت، ارتعاش)، نوع فرآیند صنعتی (پیوسته، ناپیوسته، دفعهای)، شرایط عملیاتی خاص (فشار، دما، نوع سیال، مواد خورنده) و استانداردهای مربوط به ایمنی و کیفیت باشد. برای مثال، اگر پروژه در محیطی با دمای بسیار بالا یا رطوبت شدید اجرا میشود، انتخاب تجهیزات مقاوم به حرارت یا ضد رطوبت اجتنابناپذیر است.
همچنین، در فرآیندهایی که با مواد شیمیایی خورنده سروکار دارند، تجهیزات باید مقاومت شیمیایی بالایی داشته باشند. لازم است مشخص شود که چه نوع سیگنالهایی (مانالوگ، دیجیتال، پالس) برای ارتباط بین تجهیزات و سیستم کنترل مرکزی مورد نیاز است و ابزار دقیق انتخابی باید قادر به ارائه این سیگنالها با دقت و پایداری بالا باشد. عواملی مانند پایداری بلندمدت، تکرارپذیری اندازهگیری، نیاز به کالیبراسیون مجدد، و توانایی کارکرد در شرایط دینامیکی نیز باید به دقت تحلیل شوند.
این تحلیل جامع همچنین باید شامل بررسی استانداردهای ملی و بینالمللی مرتبط با ایمنی و کیفیت تجهیزات باشد تا اطمینان حاصل شود که تجهیزات انتخابی با تمامی الزامات قانونی و عملیاتی مطابقت دارند.
۲. تعیین نوع سنسورها و پارامترهای مورد پایش: قلب فرآیند اندازه گیری
انتخاب سنسور مناسب، یکی از حیاتیترین مراحل در فرآیند انتخاب تجهیزات ابزار دقیق است. سنسورها به عنوان نقطه آغازین جمعآوری دادهها برای پایش و کنترل فرآیندها عمل میکنند و صحت انتخاب آنها تأثیری مستقیم بر کیفیت و دقت کنترل فرآیند دارد.
نوع پارامترهایی که قصد اندازهگیری آنها را دارید (مانند فشار، دما، جریان سیال، سطح مایع، یا ترکیبات شیمیایی)، به طور مستقیم نوع سنسور مورد نیاز را تعیین میکند.
برای مثال، برای اندازهگیری فشار، انواع مختلفی از سنسورهای فشار (مکانیکی، الکترونیکی، نوری) موجود هستند که هر یک ویژگیها و دقتهای متفاوتی دارند. انتخاب بهترین سنسور فشار باید با توجه به نوع سیال، دمای عملیاتی، فشار کاری و دقت مورد نیاز انجام شود.
علاوه بر این، دقت و بازه اندازهگیری سنسور بسیار مهم است؛ دقت سنسور باید متناسب با حساسیت فرآیند باشد، و بازه اندازهگیری باید تمامی محدوده تغییرات پارامتر را پوشش دهد. پایداری سنسور در طول زمان، حساسیت به شرایط محیطی (مانند تغییرات دما و رطوبت)، سرعت پاسخدهی و مقاومت در برابر نویزهای محیطی نیز فاکتورهای تأثیرگذار دیگری هستند.
۳. بررسی دقیق محیط عملیاتی و شرایط فرآیندی: تضمین دوام و کارایی
تطبیق تجهیزات ابزار دقیق با شرایط محیطی و فرآیندی خاص، کلید دوام و کارایی بلندمدت آنهاست. عواملی نظیر دما، رطوبت، لرزش، میزان خوردگی و حتی تابش مستقیم نور خورشید میتوانند بر عملکرد و طول عمر تجهیزات تأثیر بگذارند.
برای مثال، در محیطهای با خاصیت خورندگی بالا، باید از مواد مقاوم در برابر خوردگی مانند فولاد ضد زنگ خاص، تیتانیوم، یا پوششهای محافظتی استفاده شود. در محیطهای با گرد و غبار شدید یا خطر انفجار (آتشزا)، استفاده از سنسورهای با درجه حفاظتی بالا (IP Rating) و تجهیزات ضد انفجار (EX-proof) الزامی است.
همچنین، باید به ارتعاشات مداوم توجه داشت و تجهیزاتی با مقاومت کافی در برابر لرزش را انتخاب کرد.
در محیطهایی با تغییرات دمایی شدید، انتخاب تجهیزاتی با بازه دمایی گسترده و قابلیت جبرانسازی حرارتی اهمیت ویژهای دارد تا دقت اندازهگیری در شرایط مختلف حفظ شود. انتخاب تجهیزات متناسب با شرایط محیطی به طور مستقیم به افزایش عمر مفید و کاهش هزینههای تعمیر و نگهداری منجر میشود.
۴. سازگاری با سیستم های کنترلی موجود: یکپارچگی برای عملکرد بهینه
اغلب پروژههای صنعتی از سیستمهای کنترل پیچیدهای (مانند DCS یا PLC) بهره میبرند که تجهیزات ابزار دقیق باید با آنها سازگاری کامل داشته باشند. در این مرحله، توجه به پروتکلهای ارتباطی و نوع سیگنالهای ورودی و خروجی حیاتی است. به عنوان مثال، اگر سیستم کنترل از پروتکل Modbus استفاده میکند، باید تجهیزاتی که از این پروتکل پشتیبانی میکنند، انتخاب شوند.
همچنین، نوع ارتباطات (سریال، اترنت) و پروتکلهای خاص مانند Profibus, Foundation Fieldbus, HART, یا Ethernet/IP باید با سیستم کنترل مرکزی و سایر تجهیزات همخوانی داشته باشند.
توجه به نوع سیگنالها (آنالوگ یا دیجیتال)، ولتاژ یا جریان مورد نیاز و نرخ انتقال دادهها نیز از اهمیت بالایی برخوردار است.
انتخاب ابزار دقیقی که از پروتکلهای پیشرفته و استانداردهای صنعتی پشتیبانی میکنند، به افزایش یکپارچگی و هماهنگی بین تجهیزات و سیستم کنترل کمک کرده و از بروز مشکلات ارتباطی و ناسازگاری جلوگیری میکند. این امر به نوبه خود به بهبود قابلیت اعتماد و کارایی کلی سیستم کنترلی و کاهش نیاز به تغییرات و تنظیمات پیچیده در مرحله نصب و راهاندازی منجر میشود.
۵. تحلیل هزینه و بودجه بندی هوشمندانه: سرمایه گذاری برای آینده
هزینه همواره یکی از عوامل تعیینکننده در انتخاب تجهیزات است. چالش اصلی در انتخاب تجهیزات ابزار دقیق، دستیابی به کیفیت بالا با قیمتی مناسب است که نیازمند تحلیل جامع هزینه-فایده است.
در این تحلیل، باید هزینههای اولیه خرید، هزینههای نصب و راهاندازی، هزینههای نگهداری دورهای، تعمیرات احتمالی و همچنین هزینههای ناشی از خرابی و توقف تولید را به دقت ارزیابی کرد.
گاهی اوقات، انتخاب تجهیزات ارزانتر در کوتاهمدت، در بلندمدت منجر به هزینههای به مراتب بیشتر (مانند افزایش هزینههای تعمیر و نگهداری، کاهش عمر مفید تجهیزات، و افت بهرهوری) میشود.
بنابراین، ایجاد یک توازن دقیق بین کیفیت، کارایی و هزینه ضروری است. ارزیابی هزینههای چرخه عمر تجهیزات (Life Cycle Cost – LCC) میتواند به انتخاب بهینهتر کمک کند. این تحلیل جامع، تمامی هزینههای مرتبط با تجهیزات را در طول عمر مفید آنها در نظر میگیرد و نشان میدهد که سرمایهگذاری اولیه در تجهیزات با کیفیت بالاتر، به دلیل کاهش هزینههای عملیاتی و افزایش بهرهوری، در بلندمدت بسیار بصرفهتر خواهد بود.


استانداردها و گواهینامه ها: مهر تأیید بر کیفیت و ایمنی
هر تجهیز ابزار دقیق باید با استانداردهای صنعتی و الزامات ایمنی مطابقت داشته باشد. در زمان انتخاب، به گواهینامههای معتبر نظیر ATEX (برای محیطهای انفجاری در اروپا)، CE (نشاندهنده سازگاری با استانداردهای اروپایی)، IECEx (برای بازارهای بینالمللی) و UL (برای بازار آمریکای شمالی) توجه ویژه کنید. این گواهینامهها، تضمینی بر کیفیت، ایمنی و عملکرد موثر تجهیزات در شرایط مختلف عملیاتی هستند.
علاوه بر این، تجهیزات باید با استانداردهای خاص هر صنعت نیز همخوانی داشته باشند؛ برای مثال، استانداردهای مرتبط با صنایع غذایی (مانند GMP)، دارویی (مانند FDA) یا نفت و گاز (مانند API) میتوانند معیارهای ویژهای را برای سازگاری و ایمنی تعیین کنند. بررسی دقیق گواهینامهها و استانداردهای معتبر، اطمینان میدهد که تجهیزات انتخابی به طور کامل با نیازهای عملیاتی و شرایط محیطی پروژه سازگار هستند.
پشتیبانی و خدمات پس از فروش: تضمین آرامش خاطر
پشتیبانی قوی و خدمات پس از فروش مطمئن، از دیگر عوامل بسیار مهم در انتخاب تجهیزات ابزار دقیق است. انتخاب ابزار دقیق از تولیدکنندگانی که خدمات پشتیبانی فنی کارآمد، آموزش کامل کاربران و تأمین قطعات یدکی با کیفیت و به موقع را ارائه میدهند، میتواند به کاهش زمان خرابیها و افزایش عمر مفید سیستم کمک شایانی کند. خدمات پس از فروش باید شامل مواردی مانند نصب و راهاندازی، عیبیابی و تعمیرات فوری و بهروزرسانیهای نرمافزاری باشد.
تأمین سریع و به موقع قطعات یدکی در مواقع اضطراری میتواند از توقف فرآیند جلوگیری کرده و تأثیر مستقیمی بر بهرهوری و کاهش هزینههای عملیاتی داشته باشد. پشتیبانی ۲۴ ساعته و توانایی پاسخگویی سریع به مشکلات، به ویژه در فرآیندهای حساس و صنایع بحرانی، از اهمیت بالایی برخوردار است. انتخاب تامینکنندگانی با شبکه پشتیبانی گسترده و نمایندگیهای محلی میتواند تضمین کند که خدمات و قطعات یدکی در کوتاهترین زمان ممکن به دست مشتری برسند، که این امر به افزایش اعتماد به تجهیزات و کاهش ریسکهای مرتبط با خرابی آنها کمک میکند.
بررسی تجربیات پروژه های مشابه: درس آموختههایی برای موفقیت
مراجعه به تجربیات گذشته و بررسی دقیق پروژههای مشابه، میتواند در انتخاب تجهیزات ابزار دقیق بسیار مؤثر باشد. این فرآیند شامل مطالعه موردهای موفق و ناموفق در کاربردهای مشابه است که به شناسایی نقاط قوت و ضعف تجهیزات و بهترین روشهای پیادهسازی و استفاده از آنها کمک میکند. به خصوص در پروژههای بزرگ و پیچیده، تحلیل تجربیات دیگران و استفاده از درسآموختههای آنها میتواند از وقوع اشتباهات رایج جلوگیری کرده و کارایی کلی پروژه را به طور چشمگیری افزایش دهد.
از طریق بررسی پروژههای مشابه، میتوانید اطلاعات مفیدی درباره عملکرد واقعی تجهیزات، دوام آنها در شرایط عملیاتی دشوار، قابلیتهای تطبیقی با شرایط متغیر و نقاط ضعف احتمالی به دست آورید. این تحلیل همچنین به شما کمک میکند تا بهترین شیوههای نصب، راهاندازی و نگهداری را برای تجهیزات خود انتخاب کرده و به ارتقاء کیفیت و پایداری سیستمهایتان بپردازید.
نکات کلیدی برای انتخابی بی نقص: دقت، پایداری، پاسخ دهی و ثبات
در انتخاب تجهیزات ابزار دقیق، چهار فاکتور اساسی همواره باید مد نظر قرار گیرند:
- دقت (Accuracy): دقت بالا در تجهیزات ابزار دقیق به معنای توانایی کنترل بهتر و پیشبینی دقیقتر رفتار فرآیندها است. متناسب با حساسیت هر فرآیند، انتخاب دقت مناسب میتواند به بهینهسازی عملکرد و به حداقل رساندن خطاها کمک کند.
- پایداری (Stability): پایداری تجهیزات به معنای توانایی آنها در حفظ دقت و کارایی اولیه در طول زمان و تحت شرایط محیطی مختلف است. ابزار دقیق با پایداری بالا، نیاز به کالیبراسیون مجدد را کاهش داده و بهرهوری سیستم را افزایش میدهند.
- پاسخدهی سریع (Response Time): سرعت واکنش تجهیزات برای فرآیندهایی که نیاز به عکسالعمل فوری دارند، حیاتی است. سنسورها و ابزارهای دقیق باید به سرعت به تغییرات واکنش نشان دهند تا از نوسانات ناخواسته و تغییرات غیرقابل کنترل در فرآیند جلوگیری شود.
- ثبات (Reliability) در شرایط سخت: قابلیت اطمینان تجهیزات در مواجهه با شرایط عملیاتی دشوار (مانند دماهای بالا، فشار زیاد، محیطهای مرطوب یا خورنده) یک فاکتور کلیدی است. تجهیزات با ثبات بالا به کاهش خرابیهای ناخواسته و افزایش طول عمر سیستم کمک میکنند.
جدول تخصصی: راهنمای انتخاب تجهیزات ابزار دقیق بر اساس فاکتورهای کلیدی
فاکتور کلیدی | توضیحات تخصصی | کاربردهای صنعتی مرتبط |
دقت (Accuracy) | قابلیت سیستم ابزار دقیق در نمایش مقدار واقعی پارامترهای فرآیند با خطای حداقلی. دقت بالاتر مستقیماً به کنترل دقیقتر فرآیند و افزایش کیفیت محصولات منجر میشود و نقشی اساسی در کاهش ریسک خطاهای سیستم ایفا میکند. | صنایع دارویی، میکروالکترونیک، شیمیایی، نانوتکنولوژی، و محیطهای حساس به تغییرات میکروسکوپی (مانند تولید نیمههادیها) |
پایداری (Stability) | توانایی تجهیز در حفظ کالیبراسیون و عملکرد مداوم با دقت اولیه در طول زمان و تحت شرایط محیطی مختلف. تجهیزات با پایداری بالا هزینههای نگهداری و زمانهای توقف را کاهش داده و قابلیت اعتماد سیستم را افزایش میدهند. | صنایع داروسازی و مواد غذایی (نیازمند کالیبراسیون دقیق)، پتروشیمی (که عملکرد مداوم و پایدار بدون تغییرات فنی مکرر حیاتی است)، و هر صنعتی که به اندازهگیریهای بلندمدت و بدون انحراف نیاز دارد. |
پاسخدهی سریع (Response Time) | سرعت واکنش تجهیزات ابزار دقیق به تغییرات فرآیندی. تجهیزات با زمان پاسخدهی کوتاه در فرآیندهای پرسرعت از وقوع انحرافات بزرگ در پارامترها جلوگیری کرده و به حفظ پایداری فرآیند کمک میکنند. این عامل به ویژه در واکنشهای زنجیرهای صنعتی حیاتی است. | صنایع پتروشیمی (برای کنترل واکنشهای سریع)، کنترل فرآیندهای شیمیایی سریع، و صنایع نفت و گاز که کنترل لحظهای و جلوگیری از نوسانات غیرقابلپیشبینی را ایجاب میکنند. |
قابلیت اطمینان (Reliability) | قابلیت تجهیزات در عملکرد پایدار در شرایط عملیاتی سخت مانند دما و فشار بالا و محیطهای خورنده. تجهیزاتی که این ویژگی را دارا هستند، باعث کاهش خرابیهای غیرمنتظره و افزایش طول عمر تجهیزات میشوند، که منجر به بهبود بهرهوری کلی سیستم میشود. | صنایع نفت و گاز (سکویهای نفتی، پالایشگاهها)، صنایع معدنی، صنایع فلزی (ذوب و ریختهگری)، و محیطهای با شرایط عملیاتی دشوار که نیازمند مقاومت بالا در برابر عوامل مخرب محیطی هستند. |
تناسب با شرایط عملیاتی (Operational Compatibility) | بررسی جامع شرایط عملیاتی از جمله دما، رطوبت، فشار، و نوع سیال فرآیندی. این تناسب به اطمینان از عملکرد بهینه و جلوگیری از خرابیهای احتمالی کمک میکند و باعث کاهش هزینههای تعمیراتی میشود. انتخاب دقیق و متناسب با شرایط واقعی فرآیند، پایه و اساس موفقیت است. | الزامی در تمامی صنایع به ویژه در صنایعی که دارای تغییرات شدید محیطی و الزامات خاص فرآیندی هستند مانند پتروشیمی، شیمیایی، غذایی و دارویی. این فاکتور برای طراحی و پیادهسازی سیستمهای ابزار دقیق پایدار و کارآمد حیاتی است. |
مثال های عملی از تجهیزات ابزار دقیق و کاربردهای آنها
- سنسور فشار: به عنوان یکی از ابزارهای اصلی ابزار دقیق برای کنترل فشار در مخازن، لولهها و سیستمهای مختلف کاربرد دارد. انتخاب سنسور فشار مناسب (دیافراگمی، پیزوالکتریک، نوری) در سیستمهای فشار بالا یا در فرآیندهای گازی و مایع، برای افزایش ایمنی و کنترل بهتر فرآیند بسیار مهم است.
- ترانسمیترهای دما: ابزارهایی هستند که دمای فرآیند را با دقت و حساسیت بالا اندازهگیری میکنند. انتخاب نوع ترانسمیتر دما (مانند RTD یا ترموکوپل) باید با توجه به ویژگیهای محیط، دمای قابل تحمل و میزان دقت مورد نیاز انجام شود. این ترانسمیترها در صنایع نفت و گاز، مواد غذایی و شیمیایی برای کنترل و بهینهسازی دمای فرآیند استفاده میشوند.
- فلومترها: برای اندازهگیری میزان جریان سیالات گوناگون (گاز یا مایع) طراحی شدهاند. دقت در انتخاب فلومتر (مانند فلومتر جرمی حرارتی، کوریولیس، وورتکس یا التراسونیک) به نوع سیال، فشار و دمای محیط و میزان جریان بستگی دارد. فلومترها در فرآیندهای صنعتی، انتقال سیالات و سیستمهای توزیع انرژی برای کنترل و بهینهسازی جریان سیال به کار میروند.
- کنترلرها: وظیفه کنترل و نظارت بر پارامترهای مختلف فرآیند را بر عهده دارند و باید با نوع سنسورها و ترانسمیترهای مورد استفاده همخوانی داشته باشند. کنترلرهای پیشرفته میتوانند چندین پارامتر را به صورت همزمان تنظیم کنند و در صنایع خودروسازی، شیمیایی و پتروشیمی کاربرد گستردهای دارند.
- دتکتور گازی: به منظور شناسایی و اعلام خطر در مواقع نشتی گازهای خطرناک و سمی در محیطهای صنعتی به کار میرود. این دتکتورها بر اساس نوع گاز مورد شناسایی و شرایط محیطی انتخاب میشوند و در پالایشگاهها، صنایع شیمیایی و مکانهایی که با گازهای خورنده و سمی کار میکنند، نقشی حیاتی در افزایش ایمنی دارند.
- سطح سنج راداری: برای تشخیص دقیق مقدار موجودی مخازن و سیلوها کاربرد دارد. این لول ترانسمیترهای راداری در دو نوع (غیرتماسی و تماسی) ساخته میشوند و بهترین نوع از لحاظ فناوری دارای فرکانس ۸۰ گیگاهرتز است. هرچه فرکانس امواج رادار بیشتر باشد، شرایط مواد و محیط بر دقت اندازهگیری تأثیری نمیگذارد.
این تجهیزات دقیق، با فراهم کردن دادههای دقیق و بهروز، به ارتقاء عملکرد فرآیندها و افزایش ایمنی در محیطهای صنعتی کمک شایانی میکنند.
مشاوره تخصصی برای انتخاب تجهیزات ابزار دقیق: گامی به سوی اطمینان
در مسیر انتخاب تجهیزات ابزار دقیق، داشتن اطلاعات کامل و شناخت دقیق از گزینههای موجود، اهمیتی حیاتی دارد. هر پروژه صنعتی با توجه به فرآیندهای منحصر به فرد خود، نیازهای خاصی را میطلبد که تنها با مشاوره تخصصی قابل شناسایی و رفع است. شرکتهای پیشرو در این حوزه، با ارائه منابع فنی دقیق و پشتیبانی تخصصی، آمادهاند تا شما را در این مسیر یاری رسانند.
متخصصان این حوزه، با سالها تجربه در زمینه مشاوره و تامین تجهیزات ابزار دقیق، میتوانند با بررسی کامل شرایط عملیاتی و نیازهای فرآیندی شما، بهترین راه حلها را برای انتخاب ابزار دقیق مناسب ارائه دهند. تیمهای متخصص، از ابتدا تا انتهای مسیر، در کنار شما خواهند بود و با ارائه توصیههای کاربردی و محصولات باکیفیت، اطمینان میدهند که پروژه شما با بهترین استانداردهای صنعتی و اقتصادی به سرانجام میرسد.
اگر در فرآیند انتخاب نیاز به راهنمایی دارید یا سوالی برایتان پیش آمده است، میتوانید به راحتی با کارشناسان متخصص تماس بگیرید. همکاران ما آمادهاند تا از طریق مشاوره تلفنی، واتساپ و یا پاسخدهی از طریق فرمهای آنلاین، شما را در این مسیر همراهی کنند. انتخاب دقیق تجهیزات ابزار دقیق نه تنها به بهینهسازی فرآیند و کاهش هزینهها کمک میکند، بلکه میتواند ریسکهای عملیاتی را به حداقل رسانده و کیفیت محصول نهایی را ارتقا بخشد. برای دستیابی به چنین اهدافی، همراهی با متخصصینی که درک کاملی از نیازهای فرآیندی دارند، ضروری است.
خلاصه: کلیدهای انتخاب موفق تجهیزات ابزار دقیق
انتخاب تجهیزات ابزار دقیق، فرآیندی چندوجهی است که نیازمند تحلیل دقیق نیازهای پروژه، توجه به استانداردها و گواهینامههای معتبر، بررسی جامع شرایط محیطی و فرآیندی، و در نهایت در نظر گرفتن توازن هوشمندانه بین هزینه و کیفیت است. توجه ویژه به هر یک از این جنبهها میتواند به ارتقاء عملکرد کلی سیستم و کاهش قابل ملاحظه هزینههای جانبی کمک کند. با پیروی از مراحل و نکات مطرح شده در این مقاله، میتوانید مطمئن باشید که تجهیزات انتخابی شما بهترین گزینه برای پروژه مورد نظر خواهند بود و به عملکرد بهینه سیستم شما کمک شایانی میکنند.
همچنین، نباید از تجربیات پروژههای مشابه و نکات کلیدی مانند دقت، پایداری، پاسخ زمانی و ثبات تجهیزات غافل شد. انتخاب صحیح و آگاهانه ابزار دقیق میتواند به طور مستقیم منجر به کاهش هزینههای عملیاتی، افزایش چشمگیر بهرهوری و بهبود ایمنی کلی فرآیند شود. این مقاله با هدف ارائه یک راهنمای جامع و کاربردی برای انتخاب تجهیزات ابزار دقیق تهیه شده است و امید است که به شما در اتخاذ تصمیمی درست و سودمند یاری رساند.
اگر همچنان سوالی دارید یا نیاز به مشاوره تخصصی بیشتری احساس میکنید، میتوانید از مشاوران مجرب در این زمینه کمک بگیرید. آنها آمادهاند تا در هر مرحله از پروژه شما را پشتیبانی کنند و بهترین راه حلها را ارائه دهند.
پرسشهای متداول (FAQ) در انتخاب تجهیزات ابزار دقیق
در پروژههای با خطرات ایمنی بالا، چه پارامترهایی را باید برای انتخاب سنسورهای ایمنی در نظر گرفت؟
در پروژههایی که سطح ایمنی بالایی نیاز دارند، انتخاب سنسورهای ایمنی مستلزم توجه دقیق به پارامترهایی مانند سرعت پاسخدهی فوقالعاده، دقت بالا، مقاومت بینظیر در برابر شرایط سخت عملیاتی، و دارا بودن گواهینامههای ایمنی بینالمللی نظیر ATEX یا IECEx است. این سنسورها باید توانایی عملکرد بیعیب و نقص را در شرایط اضطراری داشته باشند و از مواد مقاوم و ویژه ساخته شده باشند تا در محیطهایی مانند فضاهای مستعد انفجار، دقت و عملکرد مطلوبی ارائه دهند. کالیبراسیون منظم و دقت در اندازهگیری نیز باید به گونهای باشد که خطاها به حداقل مطلق برسند، زیرا هرگونه اختلال کوچک در عملکرد سنسورهای ایمنی میتواند عواقب جبرانناپذیری در پی داشته باشد.
آیا سنسورهای مقاوم به خوردگی همیشه بهترین انتخاب برای محیط های شیمیایی هستند یا گزینه های جایگزین نیز موجودند؟
سنسورهای مقاوم به خوردگی معمولاً انتخابی منطقی و استاندارد برای محیطهای شیمیایی به شمار میروند، اما همیشه تنها گزینه ممکن نیستند. در برخی شرایط خاص، استفاده از سنسورهایی با پوششهای محافظتی ویژه یا به کارگیری کپسولهای حفاظتی تخصصی میتواند از نظر هزینه-اثربخشی مناسبتر باشد. علاوه بر این، در صورتی که فرآیند در شرایط خلاء انجام شود، بهتر است از سنسورهایی با مواد ساختاری مقاوم در برابر اثرات شیمیایی خاص آن فرآیند بهره گرفته شود. انتخاب نهایی به ترکیب دقیق مواد شیمیایی موجود و میزان تماس سنسور با آنها بستگی دارد و توصیه میشود با توجه به نیازهای عملیاتی خاص پروژه، تمامی گزینههای موجود به دقت ارزیابی شوند.
چگونه میتوان نیاز به کالیبراسیون مداوم تجهیزات ابزار دقیق را کاهش داد و پایداری طولانی مدت را تضمین کرد؟
برای کاهش نیاز به کالیبراسیون مداوم و تضمین پایداری طولانیمدت تجهیزات ابزار دقیق، استفاده از سنسورهایی با تکنولوژیهای پیشرفته که به پایداری ذاتی بالا و عدم نیاز به کالیبراسیون مکرر شناخته میشوند، بسیار مؤثر است. تجهیزات با پایداری طولانیمدت معمولاً در طراحی خود دارای سیستمهای جبرانساز و خودتنظیم هستند که از تغییرات ناخواسته جلوگیری کرده و نیاز به تنظیم مجدد را کاهش میدهند. همچنین، انجام کالیبراسیون اولیه با دقت بسیار بالا و استفاده از تجهیزات مطابق با استانداردهای کیفیت بینالمللی، مانند ISO 9001، میتواند به حفظ دقت و کاهش نیاز به تنظیمات مکرر در طول زمان کمک شایانی کند.
آیا استفاده از فناوریهای بیسیم در ابزار دقیق (Wireless Instrumentation) برای تمام صنایع مناسب است یا محدودیت هایی دارد؟
فناوریهای بیسیم در ابزار دقیق مزایای قابلتوجهی مانند کاهش هزینههای کابلکشی و افزایش انعطافپذیری نصب و جابجایی تجهیزات دارند، اما این روشها دارای محدودیتهایی نیز هستند. در محیطهایی با نویز الکترومغناطیسی بالا یا در فرآیندهایی که نیاز به دادههای پیوسته، بیوقفه و حساس به زمان دارند (مانند سیستمهای کنترل حلقه بسته سریع)، کارایی بیسیم ممکن است دچار چالش شود. همچنین، در محیطهای ایمن و حساس، احتمال قطع ارتباط یا تأخیر در انتقال دادهها میتواند به اختلال جدی در فرآیندها منجر گردد. بنابراین، فناوری بیسیم برای برخی صنایع مانند پتروشیمی یا نیروگاهها که نیاز به اطلاعات بسیار حساس و پایداری بینهایت دارند، ممکن است گزینه کاملاً مناسبی نباشد و نیاز به بررسی دقیقتر دارد.
در انتخاب تجهیزات برای محیطهای انفجاری، چه استانداردهایی الزامی هستند و کدامیک انتخابیاند؟
برای تجهیزات ابزار دقیق در محیطهای انفجاری، استانداردهایی مانند ATEX و IECEx الزامی هستند. این گواهینامهها تضمین میکنند که تجهیزات برای جلوگیری از تولید جرقه یا حرارت بیش از حد طراحی شدهاند تا خطرات ایمنی مرتبط با انفجار به حداقل برسند. استانداردهای دیگری مانند UL و CE به عنوان تکمیلکننده این گواهینامهها هستند و نشاندهنده سازگاری تجهیزات با معیارهای کیفی و ایمنی عمومی میباشند. استفاده از این استانداردها به کاهش ریسکهای ناشی از انفجار و افزایش امنیت محیط کار کمک شایانی میکند.
چگونه انتخاب مناسب تجهیزات ابزار دقیق در فرآیندهای بحرانی (مانند کنترل دمای کورهها) میتواند به افزایش بهره وری و کاهش ریسکهای عملیاتی کمک کند؟
در فرآیندهای بحرانی، مانند کنترل دمای کورهها، استفاده از تجهیزات دقیق و پاسخگو باعث میشود که تغییرات دما و نوسانات به سرعت شناسایی و کنترل شوند. این امر نه تنها به بهینهسازی عملکرد فرآیند و جلوگیری از اتلاف انرژی کمک میکند، بلکه به طور چشمگیری احتمال بروز خطرات ایمنی و آسیب به تجهیزات گرانقیمت را کاهش میدهد. انتخاب تجهیزات با دقت بالا و مقاومت فوقالعاده در برابر دماهای شدید، به حفظ پایداری فرآیند و کاهش ریسکهای عملیاتی کمک شایانی میکند.
چه نوع تجهیزات ابزار دقیقی برای پایش و کنترل شرایط محیطی با تغییرات شدید دما و رطوبت مورد نیاز است؟
در محیطهایی که تغییرات شدید دما و رطوبت رخ میدهد، تجهیزات ابزار دقیق باید دارای پایداری دمایی و رطوبتی بالایی باشند. سنسورهای دما با ویژگی جبران دمایی داخلی و سنسورهای رطوبتی مقاوم در برابر تغییرات محیطی میتوانند انتخاب مناسبی باشند. استفاده از تجهیزاتی با قابلیت تنظیم خودکار یا مقاومت بالا در برابر شوکهای حرارتی و رطوبتی نیز به افزایش دقت و کارایی آنها در چنین محیطهایی کمک میکند.
چرا سنسورهای دارای گواهینامههای مخصوص (مانند ATEX یا IECEx) برای پروژههای خاصی مانند صنایع پتروشیمی اهمیت دارند؟
گواهینامههای ATEX و IECEx تضمین میکنند که تجهیزات در محیطهای دارای خطر انفجار (که در صنایع پتروشیمی بسیار رایج است) ایمن عمل میکنند. در صنایع پتروشیمی که اغلب با مواد اشتعالزا و فرآیندهای با ریسک بالا سروکار دارند، استفاده از تجهیزات دارای این گواهینامهها به جلوگیری از حوادث جدی و فجایع کمک میکند. این گواهینامهها بیانگر این هستند که سنسورهای مربوطه میتوانند در سختترین شرایط، بدون ایجاد خطرات اضافی، به کار خود ادامه دهند.
در مواقعی که شرایط محیطی در طول پروژه تغییر میکند، چه روشهایی برای اطمینان از عملکرد صحیح تجهیزات وجود دارد؟
در پروژههایی با تغییرات محیطی پویا، استفاده از تجهیزات با قابلیت تنظیم و انعطافپذیری بالا اهمیت دارد. همچنین، پایش منظم و مستمر تجهیزات و اجرای کالیبراسیونهای دورهای و دقیق برای تطابق با شرایط جدید ضروری است. تجهیزاتی که دارای سیستمهای خودتنظیم و جبرانسازی خودکار دما و فشار هستند، میتوانند در چنین شرایطی بهتر عمل کرده و دقت سیستم را حفظ نمایند.
آیا تجهیزات ابزار دقیق با مصرف انرژی بهینه برای فرآیندهای طولانی مدت و پایدار وجود دارند و چگونه انتخاب میشوند؟
بله، برخی از تجهیزات ابزار دقیق به طور خاص برای مصرف انرژی بهینه و پایدار طراحی شدهاند. این تجهیزات از فناوریهای کممصرف استفاده میکنند و میتوانند برای فرآیندهای بلندمدت و مداوم مناسب باشند. انتخاب این تجهیزات نیازمند بررسی ویژگیهای انرژی مصرفی (مانند توان مصرفی)، تطابق با نیازهای پروژه، و همچنین ارزیابی چرخه عمر انرژی آنها است که منجر به کاهش هزینههای عملیاتی و افزایش پایداری زیستمحیطی سیستم میشود.
چگونه میتوان قابلیت تشخیص خرابی تجهیزات ابزار دقیق را در سیستم کنترلی ارتقاء داد؟
برای ارتقای قابلیت تشخیص خرابی در تجهیزات ابزار دقیق، میتوان از سیستمهای پایش خودکار پیشرفته و سنسورهای هوشمند با قابلیت تشخیص و اعلام خرابی داخلی استفاده کرد. این تجهیزات قادرند هرگونه تغییرات غیرعادی یا ناهماهنگی در عملکرد را به سرعت شناسایی و گزارش کنند. همچنین، استفاده از نرمافزارهای تحلیل داده قدرتمند و الگوریتمهای پیشبینی خرابی (Predictive Maintenance) نیز به تشخیص زودهنگام مشکلات و انجام تعمیرات پیشگیرانه کمک شایانی میکند.
چگونه عدم هماهنگی تجهیزات ابزار دقیق با شرایط پروژه میتواند بر دقت اندازه گیری و ایمنی فرآیند تأثیر منفی بگذارد؟
عدم تطابق تجهیزات ابزار دقیق با شرایط عملیاتی خاص پروژه میتواند به طور جدی منجر به بروز خطا در اندازهگیریها و کاهش دقت کنترل فرآیند شود. به عنوان مثال، اگر سنسوری که برای محیطهای معمولی و غیرخورنده طراحی شده است، در محیطی با دمای بسیار بالا یا مواد شیمیایی خورنده به کار رود، نه تنها نتایج غیرقابلاعتمادی ارائه میدهد، بلکه احتمال خرابی زودهنگام و کامل آن نیز به شدت افزایش مییابد. چنین خرابیهایی میتوانند به تأخیرهای ناخواسته در تولید، افزایش چشمگیر هزینههای تعمیر و نگهداری، و حتی وقوع حوادث ناگوار و خطرناک منجر شوند. بنابراین، تطابق دقیق و کامل تجهیزات با شرایط محیطی و عملیاتی پروژه، تضمینکننده دقت و ایمنی کلی سیستم است.
شرکت آرتا (نماینده رسمی CS Instruments در ایران) با اخذ گواهی نامه های معتبر بین المللی، آماده ارائه خدمات زیر به مشتریان گرامی است:
✅ فروش محصولات اصلی با گارانتی بین المللی
✅ کالیبراسیون تخصصی در آزمایشگاه های مجهز
✅ خدمات پس از فروش سریع و کارآمد توسط تکنسین های آموزش دیده
✅ مشاوره فنی رایگان برای انتخاب بهترین راهکار
چرا CS Instruments؟
- دقت اندازهگیری فوقالعاده با فناوری های اولتراسونیک و دیجیتال
- کاهش هزینه های عملیاتی با شناسایی نشت و بهینه سازی مصرف انرژی
- پشتیبانی گسترده در سراسر ایران توسط تیم آرتا
برای دریافت کاتالوگ، استعلام قیمت یا مشاوره رایگان:
📞 021-88570346
📧 info@cs-instruments.ir